Post Tensioning
Overview
There are many benefits to be gained by adopting a post tensioned approach to construction Including flexibility of design, faster construction Program and lower material costs. Over the Longer terms, it can reduce maintenance costs and offer the potential for increasing future Loading or being adapted for a change of use.
Perhaps the most dramatic example of design Flexibility is demonstrated by the use of post Tensioning where it allows very demanding geometry requirements including complex curves, variable super elevation and significant grade changes.
While for commercial building space and light can be maximized by construction of large column free spaces. A faster construction program and lower construction material cost result from reduced quantities of concrete and steel being needed for the super structure, but post tensioning can also significantly reduce the amount of ground work required. In addition, Thinner PT slabs and early strength stressing
Promotes a faster floor cycle time, allowing the Structure to progress more rapidly.
Over the longer term, post tensioned structures attract lower maintenance costs. Take a ware house floor slab, for example. A PT solution will deliver fewer joints and thus reduced joint maintenance
as well as long term durability.
The use of post-tensioning promotes as more environmentally friendly approach to construction.
In the first place post tensioned structure feature less construction materials steel reinforcement, Concrete and thus create fewer carbon emission in terms of production and transportation.
The actual construction process can also be environmentally sensitive.
Reinforced Concrete vs. Pre-stressed Concrete
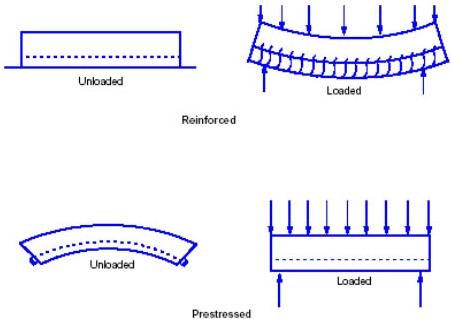
Types of Post Tensioning
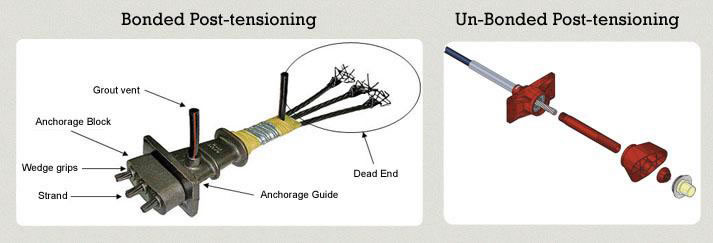
Bonded Post Tensioning System
Bonded post-tensioned concrete is a method of applying compression after pouring concrete and during the curing process (in situ). The concrete is cast around a plastic/steel/aluminum circular/flat duct. A group of tendons/wires/cables are fished through the duct circular/flat and the concrete is poured, Once the concrete has hardened, the tendons are tensioned by hydraulic jacks that react (push) against the concrete member itself. When the tendons have stressed sufficiently, according to the design specifications, they are wedged in position and maintain tension after the jacks is removed; transferring pressure to the concrete, then duct is grouted to protect the tendons from corrosion.
Un-bonded Post Tensioning System
Un-bonded post-tensioned system varies from bonded post-tensioning system by providing each individual cable coated with grease (generally lithium based) and covered by a plastic sheathing, after concreting the stressing is processed.
Post Tensioning System & Sustainability
The post-tensioned members deflect less than normal reinforced concrete; and are particularly suitable for long spans.
The advantages include:
Longer spans: The ability of post-tensioned concrete floors to achieve longer spans can reduce the number of support columns
and walls required, resulting in larger column-free spaces. In commercial buildings this is a particular advantage, permitting flexible office layouts; and typically achieving higher rental returns.
Reduced floor-to-floor height: Post-tensioning typically achieves floors of less overall depth for a particular floor loading, thus reducing the floor-to-floor height. In multi-storey construction, the resulting reduction in the height of all vertical elements gives a significant cost saving.
Superior slab deflection control: The level of post-tensioning applied to a slab can be adjusted to cater for the degree of deflection control required. This can neutralise service load deflections. There is no need for pre-cambered formwork, to cater for expected deflections;
resulting in considerable cost saving.
Efficient use of formwork: Large flat post-tensioned slabs are simple to form, due to the reduced need for step-downs in formwork at beams.
Shorter construction cycle: Appropriately designed post tensioned slabs, with high-early strength concrete, permit early stripping of formwork. Faster floor construction leads to quicker re-use of formwork, and increased speed of overall building construction.
Reduced materials handling: In comparison to reinforced concrete, post-tensioning typically permits thinner slabs, hence a reduction in concrete volume and the related materials handling, delivery trucks and pumping.
Post-tensioned concrete will result in considerable savings in materials, construction time and future maintenance costs, compared to the conventional reinforced concrete design. Thus, for the same imposed load, a more slender structure can be designed. Reduced slab depth results in reduced building height and savings in related building components. These savings translate into less material usage which means reduced embodied energy for a structure thus, creating a sustainable solution.
A study was made, buildings with post-tensioned and conventional reinforced concrete slab systems were compared. Two buildings with the same floor plans were designed using reinforced concrete and post-tensioned slab systems. The span length was chosen as 6.5 m, which is a practical limit for a relatively economical reinforced concrete solution. The buildings were designed as 10, 20 and 40 stories to demonstrate the change in material savings as the number of floors increases. Since post-tensioned slabs can be designed thinner for the same loads and spans, total weight of the structure reduces and this results in smaller columns, lower seismic loads and foundation loads. The results showed that the difference in steel material savings between conventional and post-tensioned solutions increases as the number of floors increases.
It is concluded that incorporating post-tensioning into common design practice not only reduces construction costs but also have an enhanced whole-of-life value, which, with some foresight, can enjoy extended life through reuse rather than demolition. It reduces embodied energy by using less material and produces a sustainable structural design.
There is increasing awareness of the need to provide sustainable buildings. Post tensioning system can be the choice for sustainable
development.